Ship Concept 2030: Tomorrow’s skillsets at sea

What will crew need to be adept at when stepping onboard a newbuild coming out of a yard in 2030?
E-fuels, biogas, biofuels, fuel cells, nuclear propulsion, kite sails, rigid wing sails, Flettner rotors, air lubrication, Mewis ducts, hull antifouling, onboard carbon capture, artificial intelligence and automation – there’s a huge amount of new ‘stuff’ for the world’s seafarers to get their heads around in the coming years. New skillsets and mindsets will be required to navigate shipping’s future.
DNV‘s recently published Maritime Forecast to 2050 made the good point that given the competition from other industries for limited amounts of green fuels by 2030 – a year where more stringent environmental benchmarks kick in – shipping must focus beyond fuels, in particular on what can be done now to achieve energy efficiencies and carbon emission reductions.
“The 2020s marks the decisive decade for shipping. Securing greener fuel supply is critical. However, focusing on fuels alone can distract us from making an impact this decade and ambitious future declarations are not good enough. What we need is tangible actions that will reduce emissions. Energy efficiency measures can deliver decarbonisation results now and towards 2030,” says Knut Ørbeck-Nilssen, the CEO of DNV Maritime.
Handling advanced tech
As the previous Digital section of this magazine makes clear, a lot more tech is going to be installed on newbuild ships come 2030.
As ships adopt new navigation and propulsion systems as well as alternative fuels, crewmembers will need to be trained in the operation, maintenance, and troubleshooting of these technologies.
“This,” says Morten Langthjem, chief commercial officer at Glander International Bunkering, “will undoubtedly involve a shift from traditional mechanical skills to more specialised technical and operational expertise related to alternative fuels and hybrid systems.”
Crewmembers will also require a deeper understanding of environmental regulations, emissions control, and waste management, he reckons.
“Onboard, crewmembers will need to be comfortable with advanced technology and able to manage and troubleshoot automated systems. Skills in data analysis, cybersecurity, and remote operations management will become increasingly important,” says Kishore Rajvanshy, managing director of Fleet Management, one of the world’s largest shipmanagers.
Sandith Thandasherry, the CEO of Oceanix, a data science solutions provider, puts it simply.
“The maritime workforce of 2030 will need to adapt to a more technology-centric environment,” he says, adding: “Proficiency in managing and troubleshooting automated systems, data analysis, and software maintenance will be crucial.”
According to Thandasherry there will be an increased demand for engineers and technicians with expertise in automation and digital systems, as well as data analysts who can interpret the vast amounts of information generated by onboard sensors and systems.
Onshore operations
Skillsets are going to be more diverse with a crew having more training and experience with new technologies such as augmented and virtual reality, video, and remote surveys, predicts Patrick Ryan, chief technology officer at ABS.
“One way this could manifest,” he says, “is where highly experienced crewmembers might remain onshore, and be virtually present and deployed on multiple ships manned with skilled, but less experienced, crew.”
This theme is one that has been exercising Raal Harris and all his team at Ocean Technologies Group (OTG) day in, day out for years. Harris is chief creative officer at OTG, the world’s largest crew management software provider.
“The first point,” he says, discussing ship operations in 2030 with Splash, “is to anticipate a much closer coming together of the shore and shipboard team. It is likely that some roles and operational task will move ashore. We may see a small reduction in crew but those left will need to be highly skilled.”
Harris advises that organisations will need to think about how they manage their workforce and workforce competency in a much more holistic way.
“Traditionally we have front loaded seafarer competency, but the pace of change will mean that new skills will be needed on a continual basis. So life-long learning and learning in the flow of work will be the norm,” Harris predicts.
Agreed with all the comments thus far, Heidi Heseltine, who heads up Halcyon Recruitment, argues that inter-personal skillsets will also need to be developed to ensure working environments onboard are inclusive, and physically and psychologically safe.
The shipowner perspective
Providing the shipowner perspective on how seafarers will need to have adapted by 2030 is Ralph Juhl, head of technical at product tanker giant Hafnia, who narrows the discussion down to two urgent skillset changes, namely the handling of new fuels and electronic handling of equipment.
New fuels in 2030 will mainly be gases, he reckons. “This means there is an introduction of a huge range of new technologies and equipment, plus the fact that it is highly complicated to load/bunker, maintain and handle while oil is very simple and can be done by most people,” Juhl observes, a point also picked up by Alfonso Castillero, the CEO of the Liberian Registry, the world’s largest flag, who voices his concern in particular about ammonia, an “extremely toxic and corrosive” fuel.
Turning to his second point, Hafnia’s Juhl says shipboard equipment is being more and more electronically controlled and operated which means that computer operation with back-up systems and use of service engineers or shore-based distance support are becoming the norm while the former important mechanical skills are becoming less important.
“Think of your car, 30 years back many could do repairs themselves while it is impossible today as everything is computerised,” Juhl tells Splash by way of illustrating his onboard point.
Traditional skills still required
For all the talk above some might be forgiven for thinking tomorrow’s sea workforce would be totally divorced from the current generation, something Fleet’s Rajvanshy is keen to dismiss.
“The importance of traditional seafaring skills should not be underestimated,” says the veteran shipmanager, who is now in his mid-70s, having first gone to sea in the late 1960s.
“Despite the rise of automation, the need for crewmembers who understand the sea, weather, ship handling, and mechanical systems will always remain. These skills are critical for safety and handling situations that automated systems might not be able to cope with,” Rajvanshy argues, concluding: “Therefore, in our industry automation doesn’t mean job losses – rather, roles will change and evolve. There will always be a need for skilled workers to design, build, maintain and operate the automated and AI-driven systems onshore and onboard.”
This article is one of many in the recently published Ship Concept 2030 magazine, a publication designed to give readers a realistic idea of what newbuilds will look like in seven years’ time. Splash readers can read the full magazine for free by clicking here.
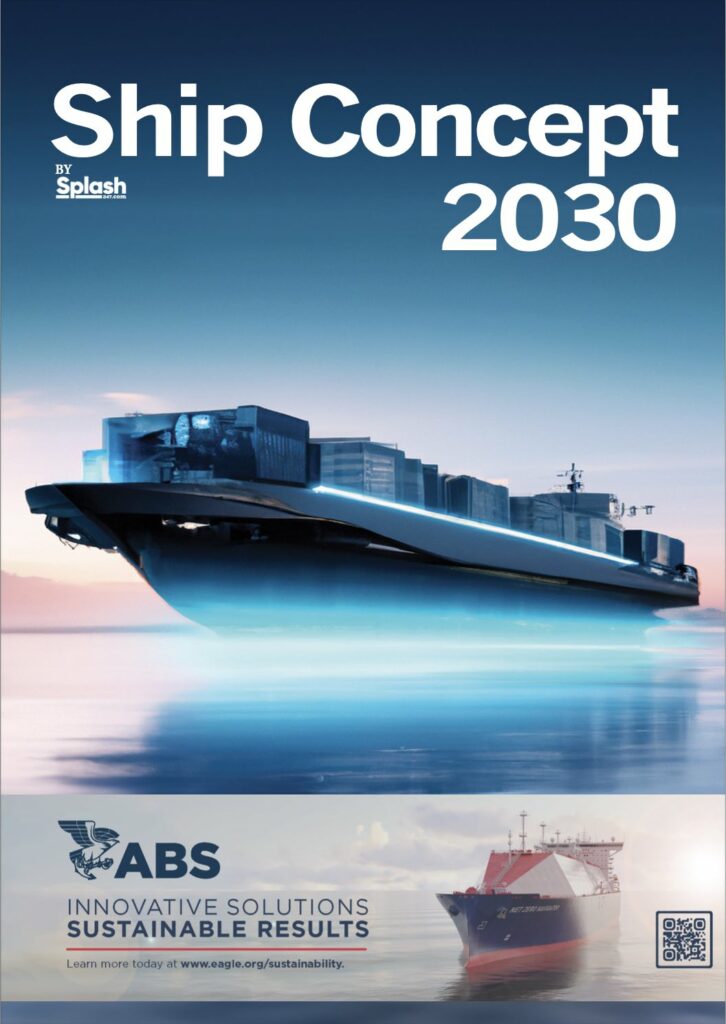
Ship Concept 2030 is sponsored by ABS, click here to read ABS’s 2023 Outlook.
“It is found that anything that can go wrong at sea generally does go wrong sooner or later, so it is not to be wondered that owners prefer the safe to the scientific….Sufficient stress cannot be laid on the advantages of simplicity. The human factor cannot be neglected in planning machinery. If attention is to be obtained, the engine must be such that the engineer will be disposed to attend to it.”
Alfred Holt, 1877.
Well said Terry