Staxxon: Solving the empty container riddle
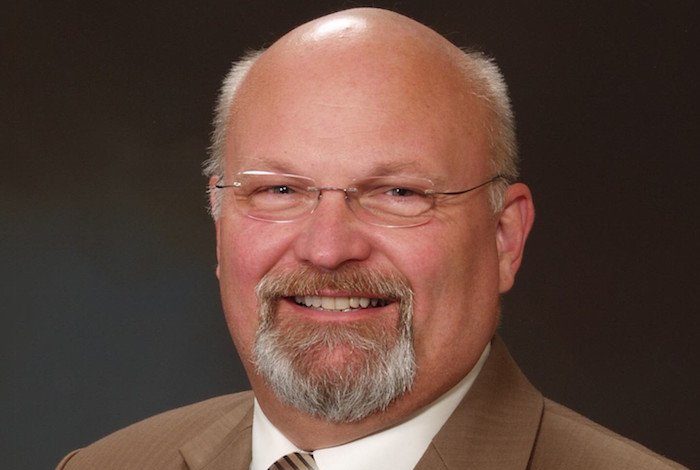
How to handle empty containers? This headache has long vexed carriers and ports alike. George Kochanowski, ceo of US firm Staxxon, is adamant he has the solution with his patented folding containers.
Collapsible containers are nothing new – it’s just that previous designs have never taken off. Kochanowski reckons he might have cracked this impasse.
“Prior to Staxxon,” he tells Maritime CEO, “all folding containers were modeled after the collapsible flat-rack styled container, certainly offering some advantages, but they also came with severe limitations which ultimately led to them being largely impractical and unusable in large scale.”
Staxxon approaches the container not as a commodity but as a technologically advanced, value added asset, Kochanowski says.
Beyond the unique upright folding feature, Staxxon has addressed the most common maintenance and repair issues of a standard container that could significantly reduce out of service time and expense. As an example, Staxxon attaches its rear doors via shoulder bolts mounted on the inside of the container and has completely re-engineered the common rear J-post assembly. This allows for a door to be replaced in minutes instead of days, as there is no need to cut away the old hinges to replace the door and then weld in new ones onto a misaligned J-post.
Five Staxxon boxes fold together into the space of a typical normal container (see image below).
“Put all these pieces together, the industry can avail itself of a more durable container, that will last longer, cost less to maintain, all the while lowering the cost of repositioning when empty by being folded, and even offers a solution to the new SOLAS mandates,” Kochanowski says, while admitting: “Yes, it will be somewhat heavier and initially cost more, but it offers a very attractive return on investment, whereas today’s container is but an unyielding and ever growing operating expense.”
A series of demonstrator sets of 20 ft and 40 ft boxes are now being manufactured in Poland and are targeted to be used on a route from Europe to Africa in the second quarter.
“Our goal is to certify other manufacturers around the globe in order to meet anticipated regional market demand,” Kochanowski says.
Ultimately, Staxxon is looking to partner strategically with ocean carriers and terminal operators.
Neat idea but someone needs to do some major number crunching to see if this will ‘stack up’. Will increased outlay and i presume increased maintenance costs over its lifetime save more than the saved lifting charges at ports. Personally i suspect not, I guess it will cost more in time and lifting costs to block 5 of these into 1 TEU than the major lines will pay a port to lift on 5 empty boxes onto their boats.
Of course if the ports lift fewer empty containers, will they have to adjust their charging structures to compensate with the loss of a serious amount of their business?
In most cases the boat is making the return trip, weather it carries 100 or 500 empty boxes the shipping line is paying for that trip regardless. This i assume would only come into its own all trips on a vessels route are at capacity (and in the current and medium term climate, surely most lines lucky enough to face that situation can just throw a few of their parked up boats at the problem?)
The concept from the ship’s point of view is brilliant. The ship on berth can be backloaded in a 1/5th of the time it takes currently. “But”…..saving money? No. The cost of handling a ‘package’ of folded containers at the yard by longshore gangs on the dock or within terminal will be an added cost. If the ‘packaging’ of MT boxes can be done off site and delivered to the port already folded and ready to be handled routinely by dockworkers, then fine. But now that is an added cost to shipper and time and space and equipment needed to do the job (or trucking/drayage company). Large operators, no problem. Small businesses, hard to do. Finally, what can one realistically expect with regard to air tight seal for goods like foodstuffs or other items where infestation is an issue. Today’s hard containers manage a pretty good degree of quality with respect to keeping your goods inside clean, dry, and free of bugs getting in. Does a “folding” box offer the same degree of seal? Certainly all goods do not require this, but it’s definitely a consideration. Great concept for many users/shippers. But not suitable for all I think.